Mirzaeifar builds strength into 3D-printed metals at the microscale
September 29, 2021
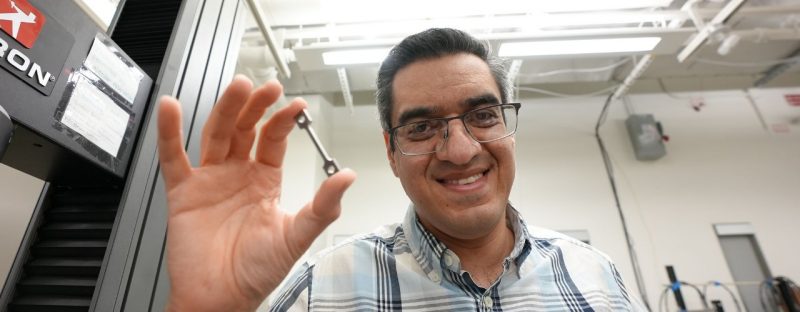
An associate professor in mechanical engineering is exploring the microstructures that give strength and ductility to metal objects. Bringing together design with 3D printing methodology, this project has been funded for a total of $500,000 by the Office of Naval Research (ONR).
The advent of 3D printing has created a new dimension for industrial design. Whereas 30 years ago metal pieces were cast in a mold that had a limited capacity for design, creating a piece with a pre-designed microstructure provides a much higher level of customization. The best methods in the past have created strong metals by subtractively creating metal pieces (using lasers to cut away pieces, similar to wood carving) but the ability to create metal pieces additively (micron drops at a time, building from the bottom up) have been a greater challenge. Fusing together these micron drops to create a structure as strong as molded metals or subtractively lasered metals has required more work.
Reza Mirzaeifar, associate professor in mechanical engineering, is putting his resources into motion to make that happen. His goal is to close the gap between the strength, ductility and reliability of traditional molded metals, taking advantage of the qualities that define additive manufacturing.
When metal 3D printing is engaged, metal powders are melted into shapes, allowing for a wider range of things like porous structures and complex geometries. 3D printers lay down tiny parts of metal with controllable microstructure, forming curves and cavities in a precise process. The formation of these structures at the microscale creates the opportunity to use that small structure to tailor strength and ductility at the small scale that compounds up to the large scale.
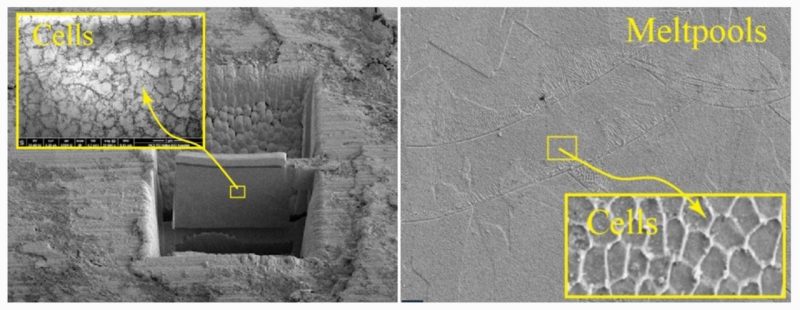
Mirzaeifar’s research goes beyond design. Not only can 3D printing engineer complex shapes, but strategic placement of materials can also add strength and ductility at strategic points. Combining the complex geometry uniquely possible through 3D printing with intricately engineered microstructures is a formula for unparalleled mechanical properties and design customization.
“3D printing of metals will be soon admitted as one of the main methods for manufacturing different devices in a broad range of industries,” said Mirzaeifar. “In each application, a different set of mechanical properties will be needed, and using the microstructure to tailor those properties will be an unmatched tool. This research will facilitate finding a comprehensive framework to pre-set the processing parameters during 3D printing to obtain a designed microstructure which will result in manufacturing the part with a pre-defined combination of mechanical properties.”